In an article published in Raconteur’s “Future of Manufacturing’, John Mason discusses how manufacturing firms have turned to data analytics and artificial intelligence and asks how many are failing to reap the rewards. What is needed is a sharper business focus to achieve expected returns.
Aside from the high-tech and leading corporates, adoption of digital technologies in the manufacturing sector remains subdued, a consequence perhaps of not seeing widespread evidence of the tangible benefits. Achieving expected returns on investment from advanced analytics and AI is less a question of technology and more a business challenge.
Success stories among early adopters are well publicised and demonstrate the advantages to be gained when the power of data from multiple sources is harnessed through expert hands and into business execution.
More precision in research and development reduces costs and increases success, product lead times can be compressed, sales and service are optimised for overall value, goods can become services, supply chain efficiencies are maximised, defects are reduced and production assets can operate at their potential.
For many though, there are “missing links” that are preventing the expected value being realised from the potential a wealth of data, analytical skills and technology are offering.
Clarity of business priorities is the starting point and that requires executive level direction. Technology has provided the toolkit, but how it should be used to best effect cannot be delegated to the IT function. The increasing presence of chief digital officers on executive teams is one trend bridging the gap between the business agenda and the role of technology.
“Generating business insight is a critical business capability that unlocks new value yet sometimes seems to be forgotten among the increasing volume of information and analysis,” explains John Mason.
Advanced analytics enable businesses to combine multiple datasets to highlight new information. The same cross-functional thinking is required in the application of this information.
For example, optimising asset performance will require co-ordinated action across production, engineering, maintenance and third-party equipment suppliers to achieve the potential performance uplift that connectivity and predictive analytics can offer. Most importantly, the business and IT functions need to work much more closely, and find a common language.
Risks associated with data security are often cited as a brake on adoption. Having a robust governance framework that defines who owns what information and how it should be used is essential.
50%
initiatives don't deliver their cost of capital
67%
companies reported human and technical capabilities as a bottleneck
Arguably the least considered aspect of a technology-led investment in data and analytics is the practicality of turning insights into measurable results. Success requires organisations to have the capabilities to act on and implement changes. The ability to test, learn, adapt and adopt is needed at all levels, and information needs to be made available to those who are going to use it in a way that is practical. Implementing minimum viable products and adopting “fast-fail” approaches that can quickly demonstrate impact are not widely established practices in many organisations.
Operating models and processes need to be capable of accommodating evolving knowledge, and the perceived threat that time-served, experienced staff may feel need to be overcome. “The expectation that the whole organisation will automatically see the benefits is likely to be unfulfilled. Involvement and ownership are key, as they are for any sustainable business change to work,” says Mr Mason.
When the links are forged for businesses to generate genuine commercial insight and swiftly translate it into action, the potential advantage of analytics will be fully realised.
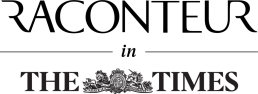
This article originally featured in Raconteur, August 2018
About the author
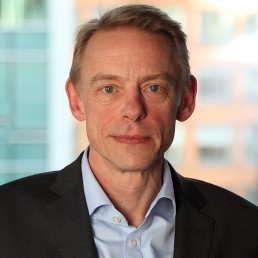
John Mason
I lead our Manufacturing practice helping clients tackle complex business challenges to achieve a step-change in outcomes, whether it be re-shaping for growth, accelerating performance improvement, or leveraging the possibilities offered by digital and automation technologies in a time of rapid evolution.