The issue
- An engineering, fabrication & assembly facility supplying deck machinery equipment to the marine industry, was severely underinvested in, with old facilities & equipment and remote from Group HQ
- Seen as a failing site with internal customers losing trust in its ability to deliver
- Disconnected planning and production functions causing late delivery and high costs
- No effective performance management system in place to drive improvements
- Very high inventories due to a lack of control of demand and production priorities
- Intention to transfer products in from Scandinavia and establish a low-cost supply centre of excellence
Solution
- Evaluation of the primary issues and development of a site transformation plan
- Focused on OTIF as the critical performance metric; established cross-functional planning with short interval control to manage demand and delivery to promise
- Improved data integrity, reset planning parameters and re-established ERP system use
- Re-organised operations to improve flow through the factory and to establish schedule adherence
- Implemented practical lean operational disciplines centred around PDCA
- Addressed excess inventory, control of stock, kitting and warehousing operations
- Established effective performance management across all functions
- Coached management to develop capability and establish sustainable improvement
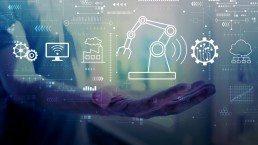
The results
- Delivery performance improvement OTIF from 14% to 95% within six months
- 45% reduction of inventories within one year
- Jump in recovered factory revenues from effective demand management & increased delivery to commitments
- Engaged and productive workforce with a clear understanding of what was required of them
- Successful capital upgrade completed while continuing to supply
- Site was established as a Centre of Excellence for deck machinery and achieved Group award for excellence
- Asked to repeat a similar exercise at another site in the Far East
An award-winning team
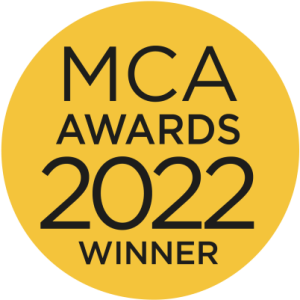
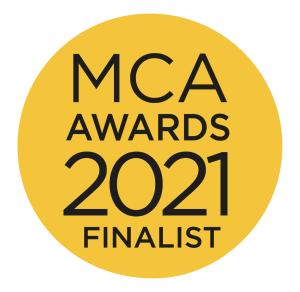
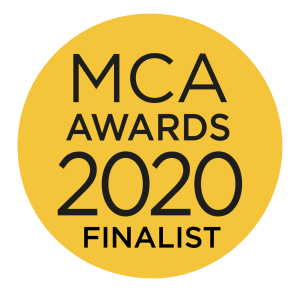
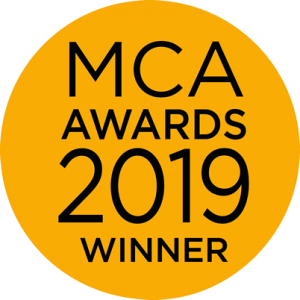
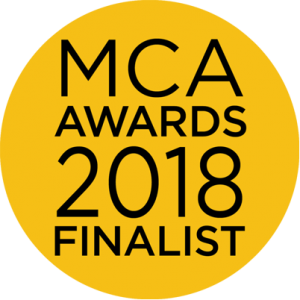
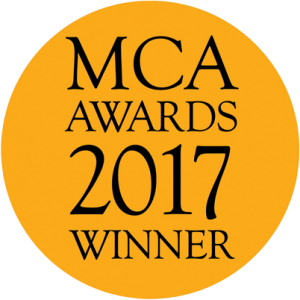
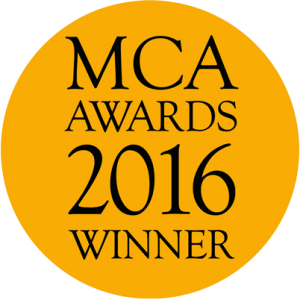
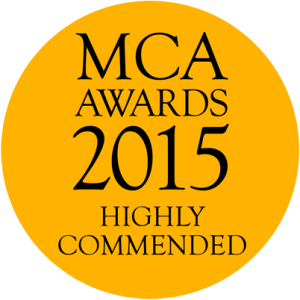
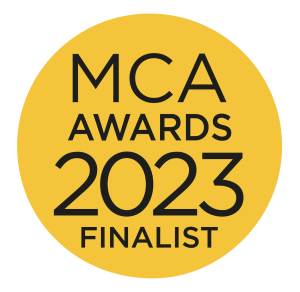
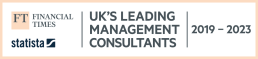
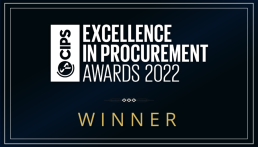