The issue
- £1billion division split into 6 semi-autonomous business units, spending £450m per annum on materials and sub-contracted services
- Each business unit under revenue and margin pressure especially those dependant on public sector work
- By re-establishing good procurement practices a modest 3% savings target was agreed upon, the stretch being that the full cash saving had to be delivered in-year
- No single picture of procurement spend or performance compared to the external market
- Procurement & supply chain savings were already baked into business unit budgets and there was pressure from plc to deliver over and above this
Solution
- Created a definitive ‘spend cube’ and with it a single set of numbers
- Completed a top-down and bottom-up analysis of spend at the detailed category/supplier level and agreed impactable spend
- Created and executed a prioritised implementation plan closely monitoring and recording the benefits as they are realised
- Redesigned the P&SC organisation bringing in the necessary skills and expertise as required
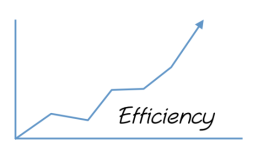
The results
- In-year cash savings of £8million with an exit run rate of £10million per annum
- New operating model fully installed and driving benefits (sustainability)
- Benefits fully traceable within business unit P&L
An award-winning team
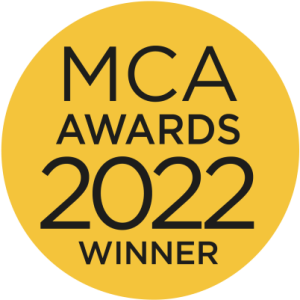
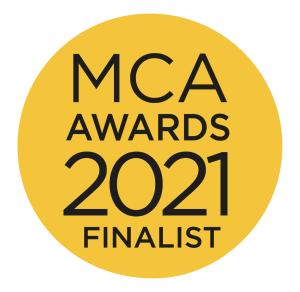
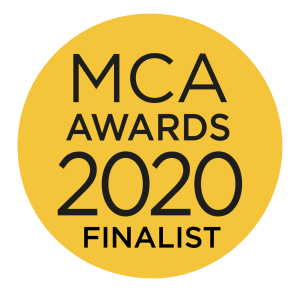
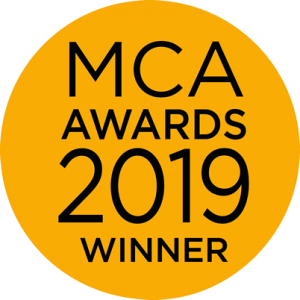
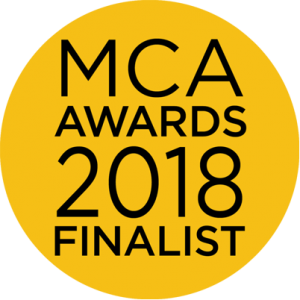
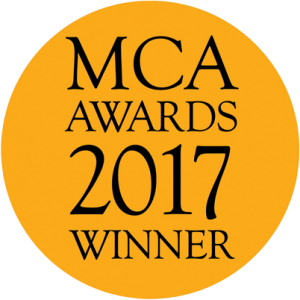
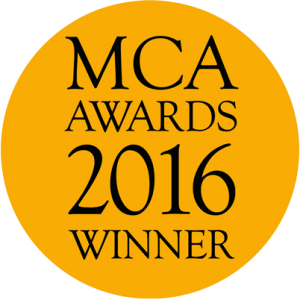
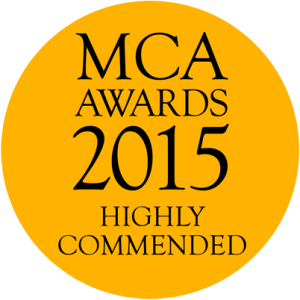
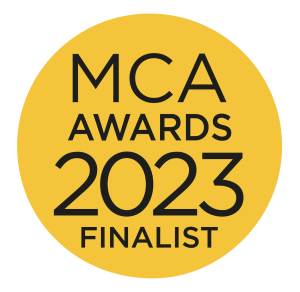
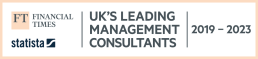
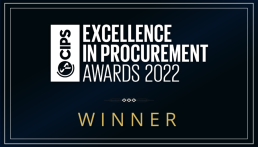